
In the competitive landscape of lens manufacturing, even minor design limitations can significantly impact product functionality and user satisfaction.We recently undertook a project to address such challenges faced by one of our esteemed clients.
In this blog, we take you behind the scenes of the redesign process, showcasing our commitment to innovation, precision engineering, and client collaboration.
Behind-the-Scenes
Challenges Faced by the Client
Our client approached us with concerns regarding their lens cap design, which hindered access to the USB charging port—a crucial feature for their product’s functionality.
Identifying this challenge required a comprehensive understanding of the client’s needs and meticulous analysis of the existing design constraints.
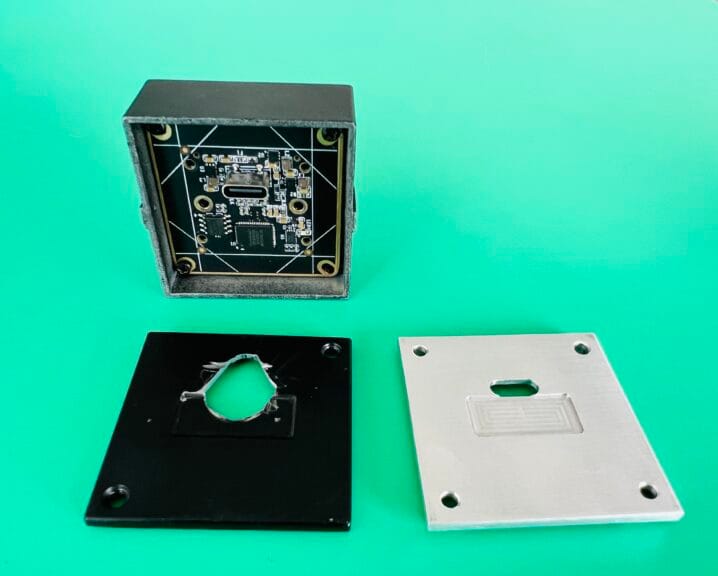
Brainstorming and Collaborative Efforts
To devise a solution, our engineering team engaged in intensive brainstorming sessions, exploring various design concepts and approaches. Ideas were meticulously evaluated, considering factors such as feasibility, manufacturability, and alignment with the client’s objectives.
Through collaborative efforts, we honed in on a solution that promised to address the client’s concerns effectively.
Technical Breakdown
Utilizing CNC Machining for Precision
Central to our solution was the utilization of custom CNC (Computer Numerical Control) parts. Learn more about the benefits of CNC machining in high-precision manufacturing. CNC machining allowed us to achieve unparalleled precision and consistency in crafting the redesigned lens cap.
The versatility of this technology enabled us to translate design concepts into tangible components with remarkable accuracy.
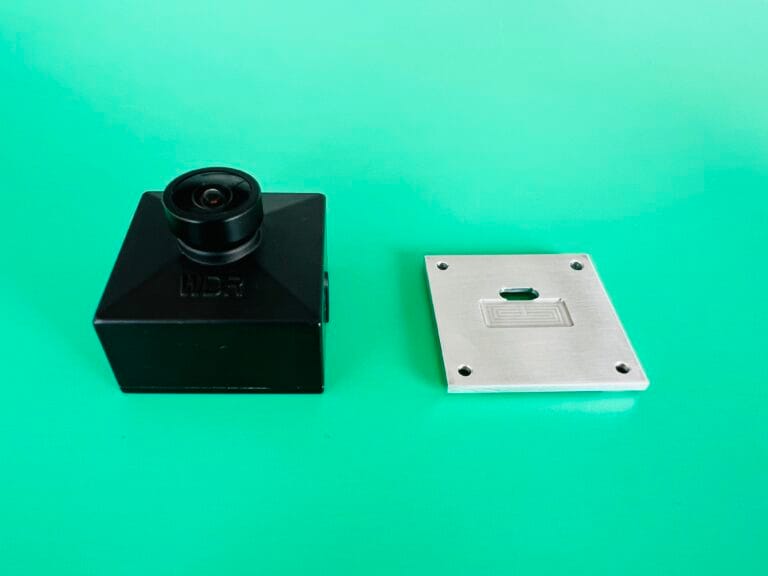
Client Collaboration
Effective Communication and Feedback Integration
Throughout the project, effective communication and collaboration with the client were paramount. Their feedback informed each design iteration, guiding our decision-making process and ensuring alignment with their vision.
Challenges encountered during collaboration were addressed promptly, fostering a collaborative partnership grounded in trust and transparency.
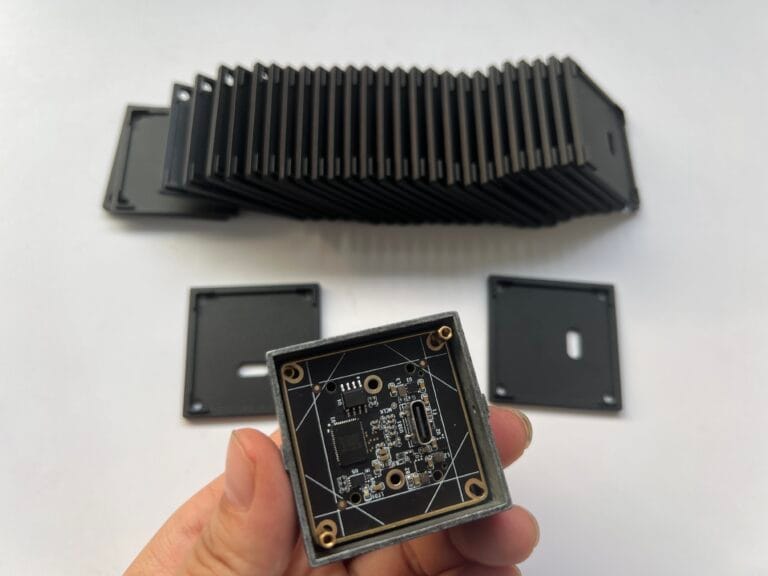
Quality Assurance
Rigorous Testing and Validation
Quality assurance remained a cornerstone of our process, with rigorous testing procedures implemented to validate the redesigned lens cap prototype. Read about industry standards for quality assurance in manufacturing.
From functional testing to durability assessments, each step was meticulously executed to ensure the reliability and performance of the final product.
Industry Standards and Certifications
Our commitment to quality and excellence culminated in the attainment of industry standards and certifications.
These accolades serve as a testament to our dedication to delivering products of the highest caliber, setting a benchmark for quality within the lens manufacturing industry.
Impact and Future Outlook
Driving Growth Through Innovation
Continuous innovation lies at the heart of our approach, driving growth and competitiveness in industries like lens manufacturing.
By staying ahead of technological advancements and anticipating evolving consumer needs, we strive to enhance product offerings and elevate the customer experience.
Long-Term Benefits for Clients and End-Users
The redesigned lens cap not only addresses immediate concerns but also offers long-term benefits for both the client and end-users.
From improved product performance to enhanced user experience, the redesigned lens cap opens doors to expanded market opportunities and heightened customer satisfaction.
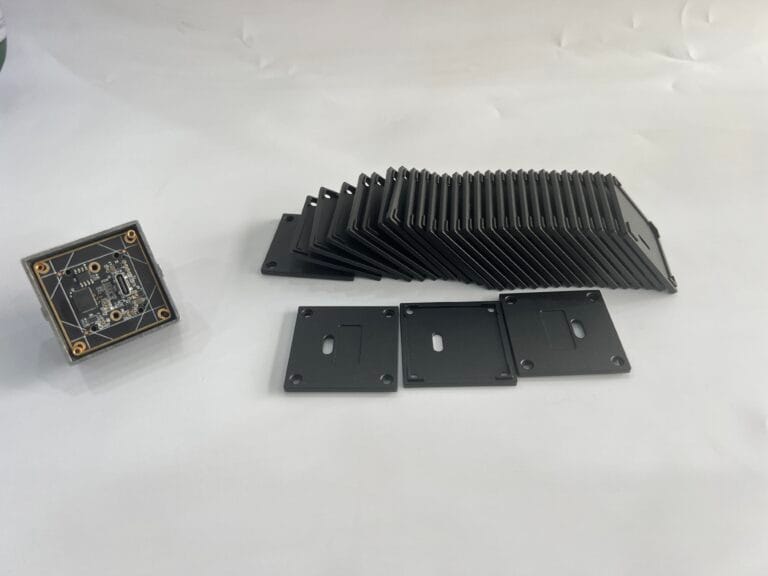
Ending
At Witcool, every challenge is an opportunity for innovation. We’re committed to serving our customers with excellence and look forward to assisting with your lens projects. Reach out to us for unparalleled quality and innovation.
FAQ
Q: What specific challenges did the client face with their lens cap design?
A: The client encountered difficulties with their lens cap design that hindered access to the USB charging port, a crucial feature of their product functionality. This limitation prompted the need for a redesign to enhance accessibility and usability.
Q: How did your engineering team approach the solution process?
A: Our engineering team employed a collaborative approach, engaging in intensive brainstorming sessions to explore various design concepts and solutions.
We prioritized effective communication and feedback integration to ensure alignment with the client’s objectives and requirements.
Q: What role did CNC machining play in the redesign process?
A: CNC machining played a pivotal role in achieving precision and consistency in crafting the redesigned lens cap. By leveraging this advanced manufacturing technology, we were able to translate design concepts into tangible components with unparalleled accuracy and quality.
Q: How did client collaboration influence the final design outcome?
A: Effective communication and collaboration with the client were instrumental in shaping the final design outcome. By incorporating client feedback throughout the project, we were able to iterate and refine the design to meet their specific needs and preferences.
Q: What quality assurance measures were implemented to ensure the reliability of the redesigned lens cap?
A: Rigorous testing and validation procedures were implemented to ensure the durability, functionality, and reliability of the redesigned lens cap prototype.
From functional testing to durability assessments, each step was meticulously executed to uphold our commitment to quality and excellence.