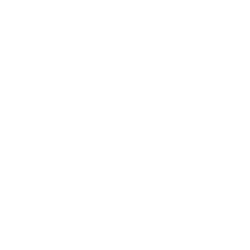
Usinage de précision pour l'automobile
- Assure des tolérances serrées et une grande précision.
- Réduit les déchets et accélère les cycles de production.
- Idéal pour les métaux comme l'aluminium et l'acier.
- Assure la cohérence dans la production de masse.
Confiance de la part de



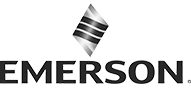
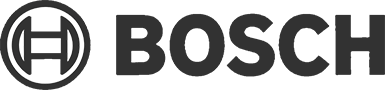
Pourquoi le prototypage est-il important dans l’industrie automobile ?
Le prototypage accéléré favorise l’avancement de la conception automobile.
Le secteur automobile est vaste et complexe, nécessitant des mises à jour de conception fréquentes et des fonctionnalités innovantes pour rester compétitif. Compte tenu de la longueur des cycles de développement des véhicules, un prototypage efficace et rapide devient essentiel. Il comble le fossé entre le développement du concept initial et la production à grande échelle, jouant un rôle essentiel dans la validation du produit.
Le prototypage permet aux équipes de conception de tester l'impact de nouveaux concepts auprès des consommateurs, de vérifier leur fonctionnalité et de communiquer efficacement leurs idées aux parties prenantes. En outre, il permet d'améliorer la conception et d'évaluer les processus de fabrication, garantissant ainsi des transitions plus fluides vers la production de masse.
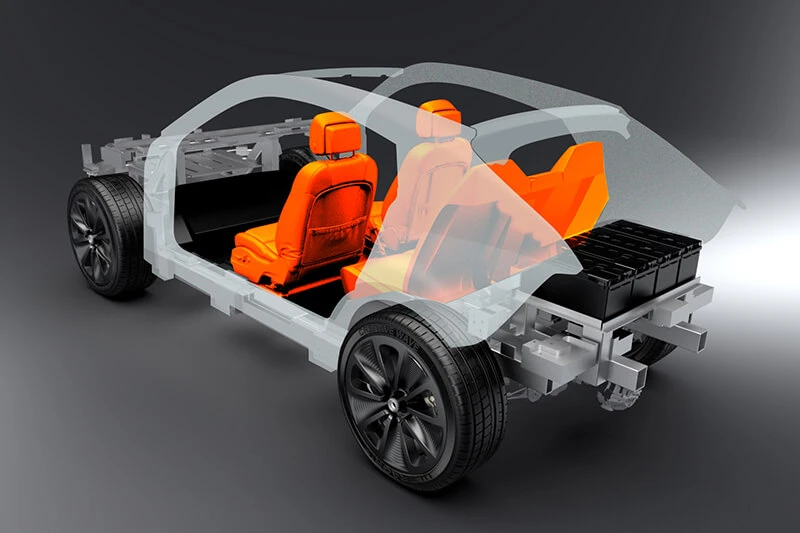
Du prototypage à la production
L'usinage CNC dans l'industrie automobile permet le prototypage rapide, la validation précise et la production en série de composants complexes tels que les moteurs et les transmissions, tout en respectant des normes de qualité strictes.
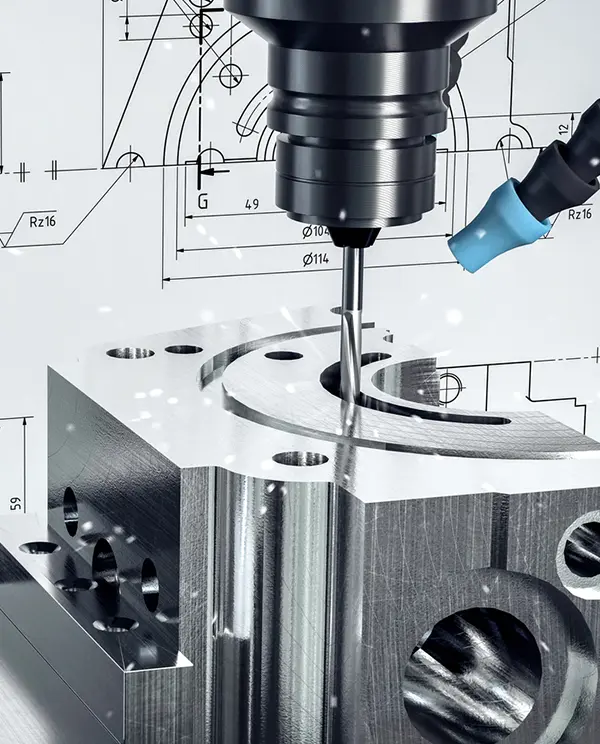
01. Prototypage
Les prototypes représentent la première étape du développement de produits automobiles. À ce stade, vous testez vos conceptions, apportez les modifications nécessaires et choisissez le matériau approprié pour les pièces automobiles. Les prototypes constituent la base du processus de développement, permettant des modifications rapides et rentables des conceptions et des matériaux. Même des formes géométriques complexes peuvent être recréées avec précision et les modèles reflètent le produit final.
- Modifications de conception et de matériaux rapides et rentables.
- Détails précis de géométries complexes.
- Les prototypes correspondent au produit final.
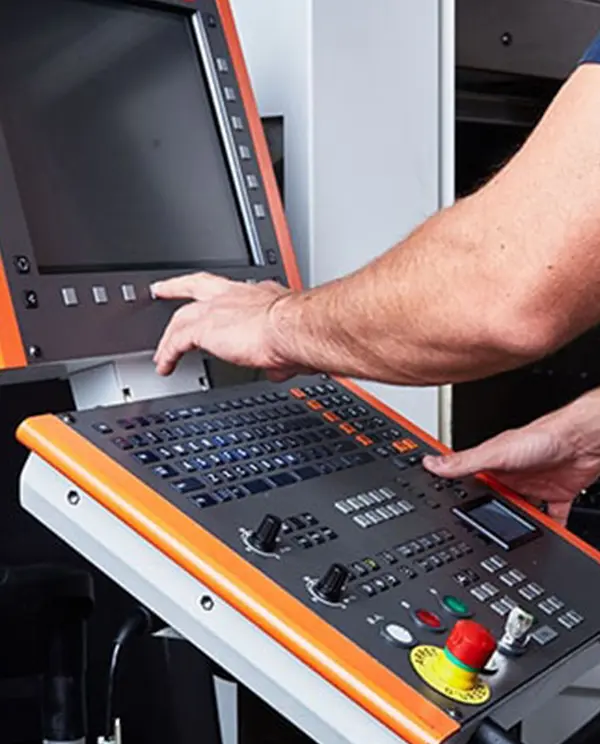
02. Validation et tests techniques
Cette étape implique des itérations basées sur les performances pour garantir que le prototype répond à toutes les exigences fonctionnelles. Chez RapidDirect, nous fournissons des prototypes fonctionnels qui facilitent l'identification et l'atténuation des risques de conception. Plusieurs itérations peuvent être nécessaires pour que le prototype final réponde à toutes les exigences.
- Assistance de conception et d'ingénierie 24h/24 et 7j/7.
- Fabrication de pièces de précision.
- Optimisation des propriétés des matériaux pour des projets personnalisés.
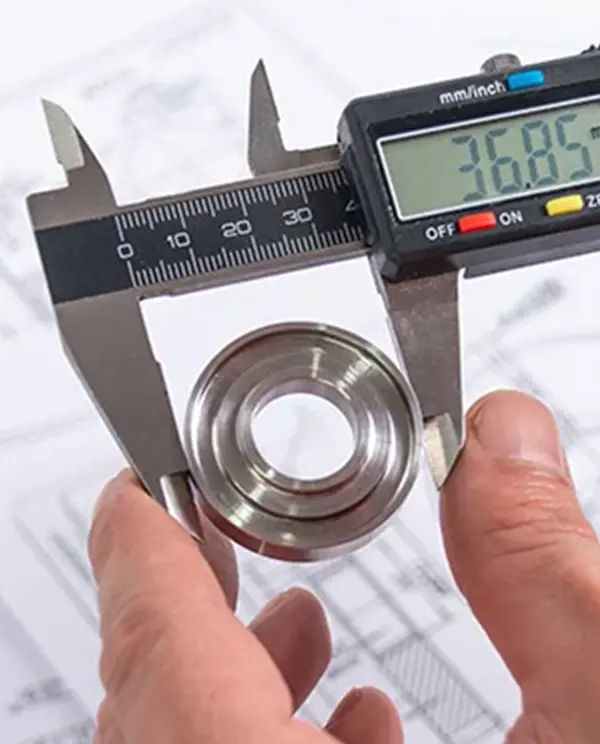
03. Validation et tests de conception
À ce stade, la fonctionnalité, l'apparence et les performances des pièces sont évaluées et testées à l'aide de divers matériaux et options de finition. Chez RapidDirect, nous proposons une large gamme de matériaux et de finitions pour répondre à vos besoins de conception uniques. À ce stade, les pièces sont prêtes pour l'évaluation des consommateurs et les tests sur le marché.
- Finitions durables et de haute qualité.
- Évaluation complète de l'apparence et des performances.
- Tests de fonctionnalité pour la préparation au marché.
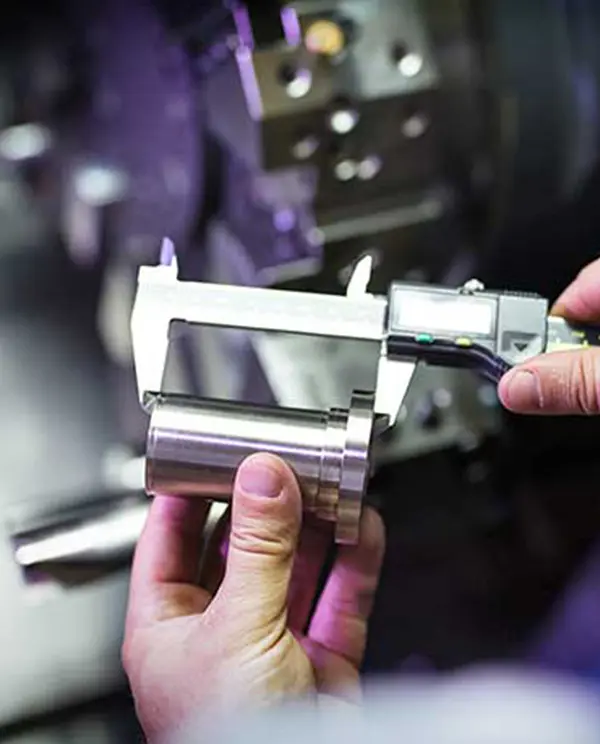
04. Validation et tests de production
Il s'agit de la dernière étape avant la production en série. PVT prépare la conception pour la fabrication à grande échelle avec des capacités de contrôle qualité et de production. Chez RapidDirect, nous collaborons étroitement avec vous, en intégrant les commentaires et en effectuant les derniers ajustements pour garantir une production efficace. Cette étape implique également la mise en place de la chaîne d'approvisionnement du produit.
- Vérification du processus de production.
- Outils pour la production en petites séries.
- Livraison rapide des composants finis.
- Test de préparation à la production de masse.
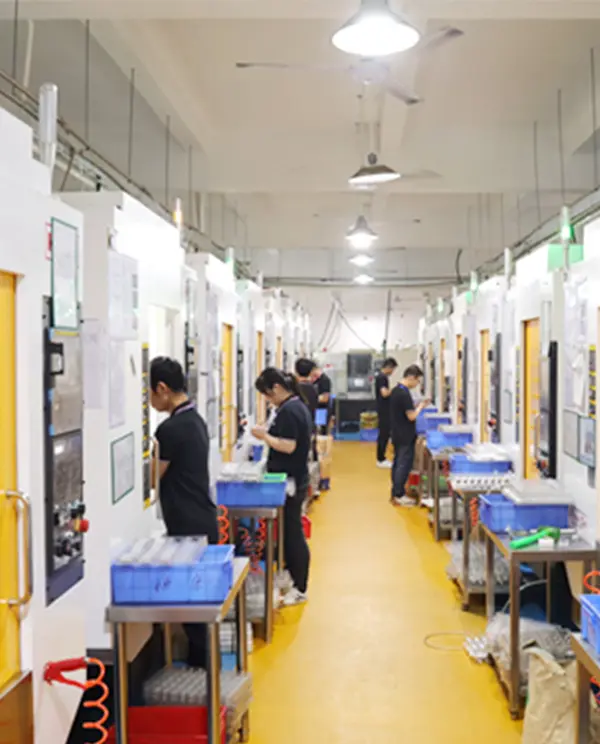
05. Production de masse
Une fois les tests du produit terminés, la production en série des composants finaux commence. À ce stade, la précision et le contrôle de la qualité sont primordiaux. RapidDirect garantit une production et une livraison rapides de pièces de haute qualité à l'aide de technologies avancées.
- Contrôles de qualité approfondis.
- Pièces de qualité supérieure.
- Opérations secondaires pour obtenir des finitions optimales.
- Les pièces de précision répondent à des tolérances strictes.
Capacités de fabrication automobile
Les spécialistes automobiles Witcool proposent un usinage CNC de haute précision, offrant des solutions personnalisées qui favorisent l'innovation et garantissent d'excellentes performances dans la production de pièces.
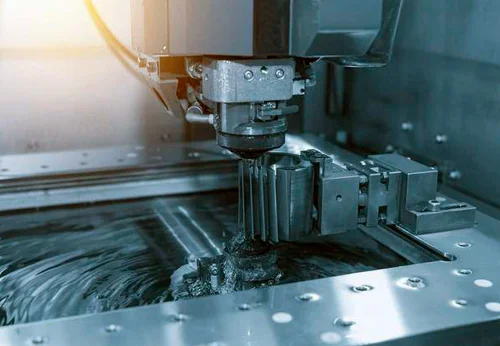
Usinage CNC
Création de structures précises et complexes par fraisage, tournage et post-traitement, parfaitement adaptées aux prototypes complexes et aux pièces métalliques fonctionnelles.
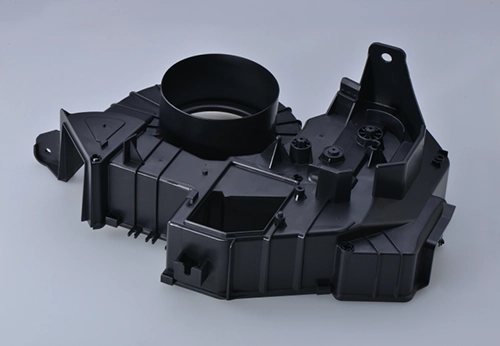
Coulée sous pression
Production rapide de pièces moulées et d'outillages intermédiaires, optimisés pour la production en série avec une qualité constante.
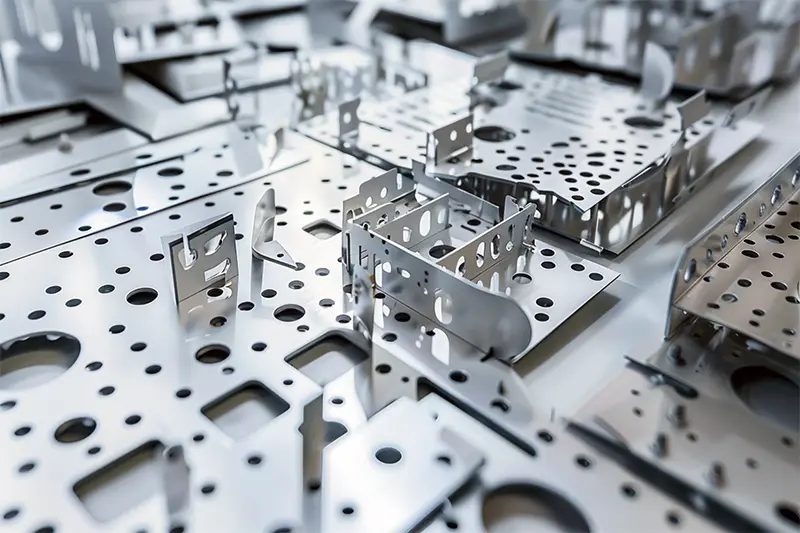
Traitement de la tôle
Offre une flexibilité dans la formation de composants métalliques précis pour diverses applications, garantissant à la fois adaptabilité et précision.
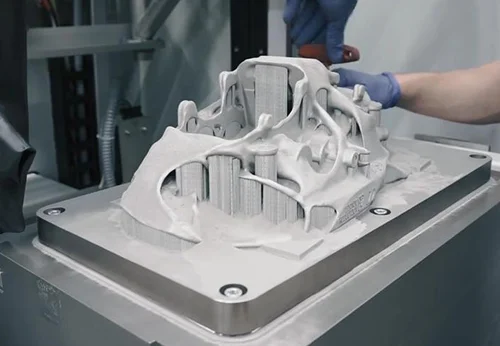
Impression 3D
Un processus rapide et polyvalent qui permet la création rapide de formes complexes à partir d'une variété de matériaux, idéal pour des conceptions innovantes.
Matériaux et finitions de surface
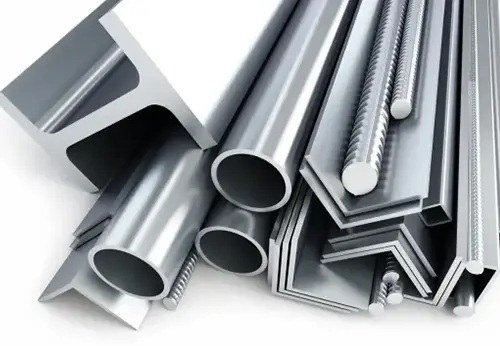
Matériels
Nous proposons une large gamme de matériaux, notamment des métaux, des plastiques et des composites.
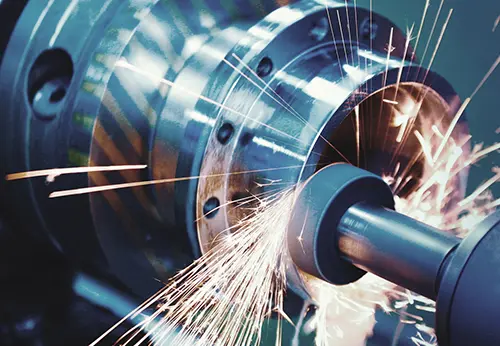
Finition de surface
Notre finition de haute qualité améliore la durabilité et l'apparence des pièces, répondant aux exigences des surfaces lisses et texturées.
Capacités de fabrication automobile
Fort de ses années d'expérience dans l'industrie automobile, Witcool a collaboré avec succès avec Toyota et Tesla, en fournissant des solutions d'usinage CNC de haute précision. Nous nous engageons à la qualité et à l'innovation, en garantissant la production de pièces automobiles complexes répondant aux normes les plus élevées et en intégrant en permanence de nouvelles technologies pour répondre aux besoins des clients.

« La collaboration avec Witcool a considérablement amélioré notre efficacité de production. Leur précision, leur approche innovante et leur souci du détail ont joué un rôle clé dans le développement de nos composants de transmission. »
Projet Toyota : composants de transmission de précision
Pour Toyota, nous avons fabriqué des composants clés de la transmission à l'aide de procédés de fraisage et de tournage CNC. Grâce à notre usinage de haute précision, Toyota a amélioré l'efficacité et la fiabilité de son système de transmission, garantissant la précision et la durabilité des pièces.
Fraisage CNC, tournage CNC et traitement supplémentaire pour améliorer la durabilité et l'efficacité.
Une réduction de 15% du temps de production et une augmentation de 20% de la durabilité des composants, permettant à Toyota d'améliorer les performances de son système de transmission.
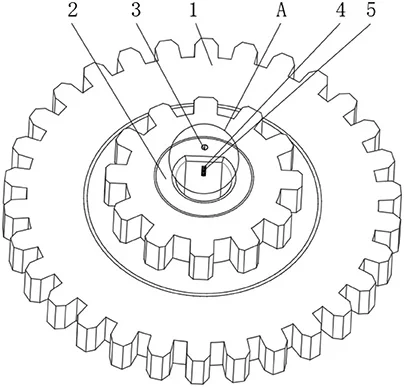
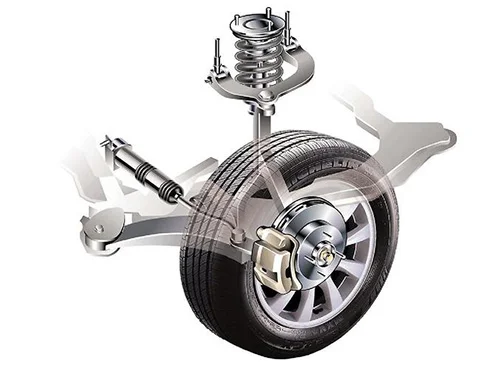

« La capacité de Witcool à fournir des composants de suspension de haute qualité a été un élément crucial du succès de nos derniers modèles. Leur professionnalisme dans l'usinage CNC et leurs solutions innovantes ont dépassé nos attentes. »
Projet Tesla : composants du système de suspension
Nous avons fourni des composants de système de suspension de haute précision pour les derniers modèles électriques de Tesla. Tirant parti de technologies d'usinage CNC avancées et d'une conception innovante, nos pièces ont répondu aux exigences de performance strictes de Tesla.
Fraisage CNC, impression 3D pour le prototypage et finition de surface personnalisée pour garantir une qualité supérieure.
Précision obtenue de ± 0,01 mm, améliorant la stabilité et les performances des véhicules Tesla.
Assurance qualité
Witcool garantit la plus grande précision et le respect de toutes les normes de qualité à chaque étape de la production. Nous respectons les réglementations internationales, notamment ISO et IATF, pour produire des composants automobiles fiables. Un contrôle qualité et des tests rigoureux garantissent que nos produits répondent aux exigences de l'industrie automobile et offrent une fiabilité opérationnelle à long terme.
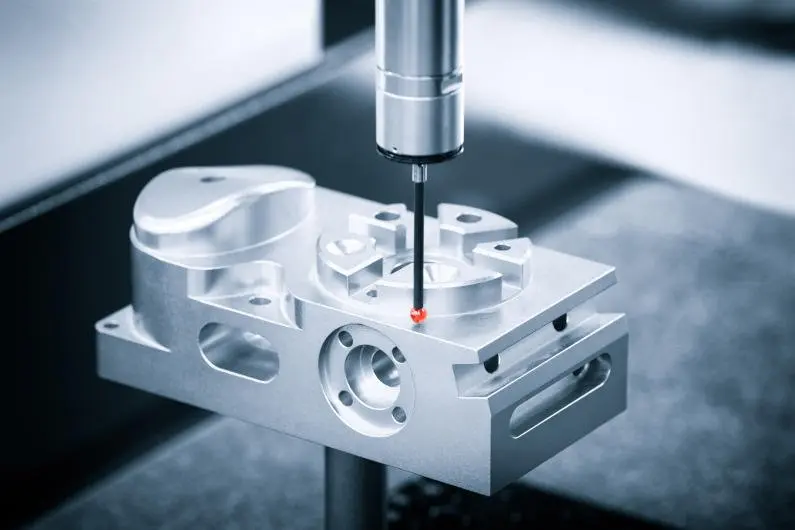
Usinage de précision et contrôle qualité
Dans l'industrie automobile, l'usinage CNC est utilisé pour fabriquer des composants critiques tels que des pièces de moteur, des éléments de transmission et des composants de suspension. Witcool met en œuvre des mesures de contrôle qualité strictes à toutes les étapes, garantissant que chaque pièce répond aux exigences de tolérance les plus strictes. Nous avons adopté un système de gestion de la qualité totale (TQM), où chaque étape de production est surveillée en temps réel pour minimiser les défauts et les erreurs. Pour garantir la précision tout au long de la production, nous utilisons des machines de mesure tridimensionnelle (CMM) et des systèmes de mesure optique.
processus de contrôle qualité :
Contrôle des matières premières :
Avant le début de la production, tous les matériaux sont soumis à des inspections rigoureuses pour garantir leur conformité aux normes de conception et aux normes de l’industrie.
Inspection en cours de fabrication :
À chaque étape critique de la production, des points de contrôle sont mis en œuvre pour éviter l’accumulation d’erreurs et assurer le respect des spécifications.
Inspection finale et vérification :
Une fois la production terminée, des contrôles approfondis des dimensions, de la qualité de surface et des tolérances sont effectués pour garantir le respect total des exigences techniques.
- Ces processus assurent une qualité maximale à chaque étape, garantissant la fiabilité du produit final.
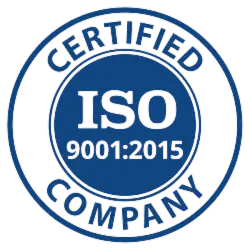
Certification et normes de l'industrie
Nos processus de fabrication sont certifiés ISO 9001 et IATF 16949 (industrie automobile), ce qui garantit que tous les composants automobiles répondent aux normes internationales de qualité. Les matériaux et les processus respectent également strictement les exigences de l'industrie, telles que RoHS et REACH, afin de se conformer aux réglementations environnementales et de sécurité.
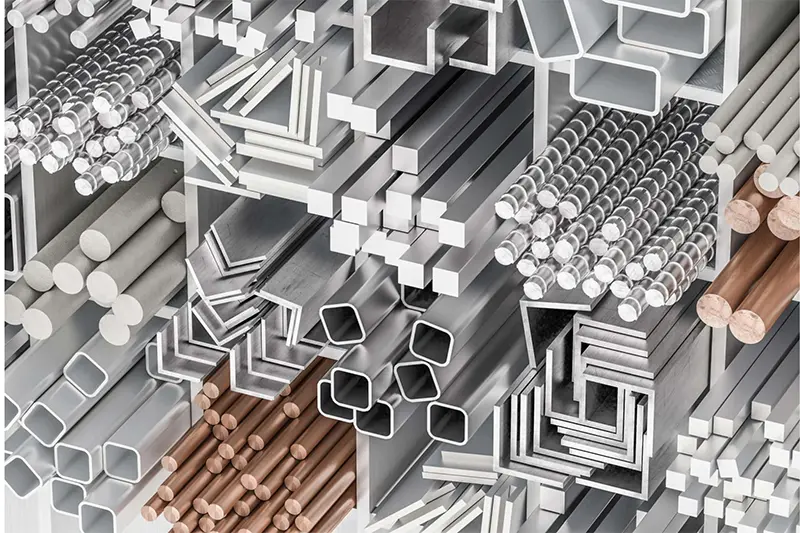
Normes relatives aux matériaux et aux procédés
Les composants automobiles nécessitent des matériaux très résistants et précis. Witcool sélectionne des matériaux conformes aux normes industrielles, tels que les alliages d'aluminium, l'acier inoxydable et le titane, et applique des paramètres d'usinage optimisés pour garantir une conformité totale aux exigences.
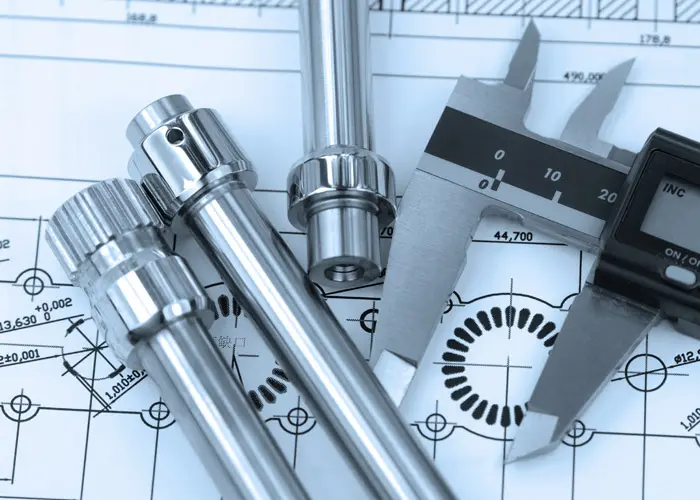
Test et vérification des produits
Witcool effectue des tests et des vérifications approfondis à chaque étape de la production, notamment des tests de fatigue, de résistance à la corrosion et de résistance aux chocs, qui sont essentiels pour les pièces automobiles. Ces tests confirment les excellentes performances et la fiabilité des composants dans des conditions extrêmes.
Processus spécifiques de test et de vérification :
Essais de fatigue :
Simule la contrainte de charge sur les composants lors d'une utilisation prolongée pour éviter toute défaillance sous tension.
Essais de résistance à la corrosion :
Évalue la résistance des matériaux à la corrosion pour les pièces exposées à une humidité élevée ou à des environnements agressifs.
Essais d'impact :
Évalue la résistance et la durabilité des composants soumis à des impacts soudains ou à une pression élevée.
Vérification dimensionnelle :
Mesure la précision des pièces à l'aide de systèmes de mesure de haute précision pour garantir la conformité avec les tolérances au niveau du micron.
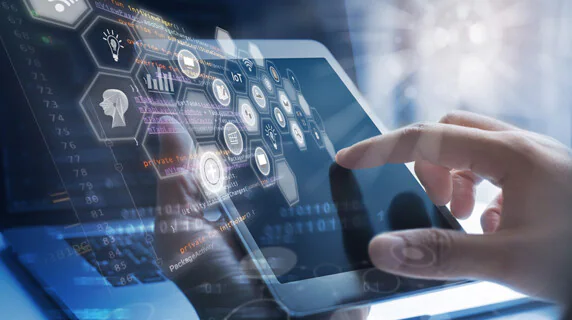
Système de suivi complet
Witcool utilise un système de suivi numérique qui enregistre chaque étape, des matières premières aux produits finis, ce qui permet de retracer les processus de production à tout moment. Cette approche assure une gestion transparente et permet de résoudre rapidement les problèmes potentiels de qualité.
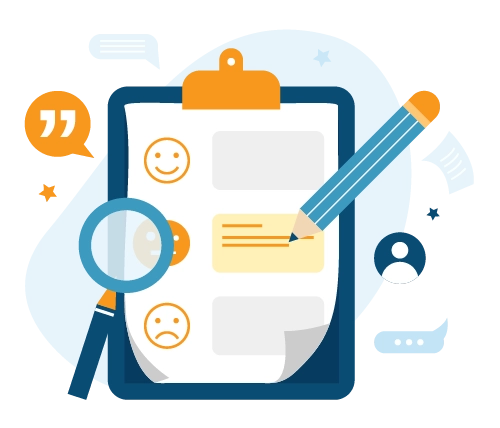
Commentaires des clients et amélioration continue
Nous prenons en compte les retours de nos clients du secteur automobile et perfectionnons en permanence nos technologies CNC. En optimisant les processus et en adoptant des méthodes d'usinage de pointe, Witcool garantit la livraison de composants automobiles répondant aux normes de qualité les plus élevées.
Questions fréquemment posées
Witcool possède une vaste expérience dans l'usinage CNC et est prêt à offrir des solutions de haute précision pour l'industrie automobile, garantissant qualité, fiabilité et innovation dans chaque projet.
Comment maintenir une haute précision dans des pièces complexes ?
Le contrôle constant des paramètres et l'utilisation de machines de haute précision permettent d'éviter les écarts de tolérance. Le maintien d'une température stable est également important pour éviter les distorsions thermiques.
Quels matériaux sont les meilleurs pour les pièces automobiles ?
L'aluminium, l'acier inoxydable et le titane sont couramment utilisés en raison de leur résistance et de leur légèreté. Le choix du matériau dépend des exigences de poids, de durabilité et de résistance à la corrosion.
Comment éviter les défauts de surface lors de l'usinage ?
Le choix des outils de coupe et des vitesses d'avance appropriés est essentiel pour éviter les défauts de surface. L'utilisation de liquides de refroidissement réduit également le risque de dommages.
Quels sont les défis rencontrés lors du prototypage ?
Il est souvent difficile d'obtenir une géométrie et une précision parfaites dans un court laps de temps. Des tests réguliers et des ajustements de processus permettent de minimiser les erreurs pendant la phase de prototypage.
Comment gérer l'usure des outils lors de l'usinage de matériaux durs ?
L'utilisation d'outils avec des plaquettes en carbure et la surveillance constante de leur état peuvent prolonger la durée de vie de l'outil. Le choix de la vitesse de coupe et de l'avance correctes est essentiel pour minimiser l'usure.
Comment assurer la répétabilité en production de masse ?
L'étalonnage régulier des équipements et l'automatisation des processus garantissent une répétabilité élevée des pièces. Un contrôle qualité à toutes les étapes de la production est également nécessaire.