Selecting the right milling technique—whether it’s 3-Axis, 4-Axis, or 5-Axis Milling—can significantly impact the efficiency and quality of your manufacturing processes. This guide will help you understand the key differences and benefits of each type, ensuring you make the best choice for your production needs.
What is CNC Milling?
CNC Milling is a machining process used in manufacturing that involves the removal of material from a workpiece using computer-controlled rotary cutters. CNC stands for “Computer Numerical Control,” which means that the milling machine is operated by pre-programmed computer software, allowing for high precision and repeatability.
The “axis” in CNC milling refers to the number of directions in which the cutting tool can move. More axes typically allow for more complex and precise cutting operations.
3-Axis CNC Milling

3-axis CNC machines are the most common type of CNC equipment. They operate along three primary axes: X, Y, and Z.
- X-Axis: Moves horizontally.
- Y-Axis: Moves vertically.
- Z-Axis: Moves up and down.
Applications:
3-axis machines are excellent for simple, flat parts that don’t require complex features or multiple faces. They’re commonly used for drilling, milling, and cutting flat surfaces. Due to their simplicity, they are cost-effective and ideal for high-volume production of straightforward parts.
Limitations:
The limitation of 3-axis machining is its inability to efficiently create parts with complex geometries. When intricate features on multiple sides of a part are required, additional setups or machining processes are necessary, which can increase production time and costs.
4-Axis CNC Milling
4-axis CNC machines operate on the same three axes as a 3-axis machine, but with an additional rotational axis, typically called the A-axis.
- A-Axis: Rotation around the X-axis.
Advantages:
4-axis machining increases efficiency by reducing the number of setups required. It also improves the accuracy of the final product since the part remains fixed in place during the machining process.
Applications:
The addition of the A-axis allows the machine to rotate the workpiece, making it possible to machine multiple sides without repositioning the part manually. This is particularly useful for machining features like holes or slots on the sides of a part. It’s commonly used in operations that require high precision and the ability to work on different sides of a workpiece without additional setups.
5-Axis CNC Milling
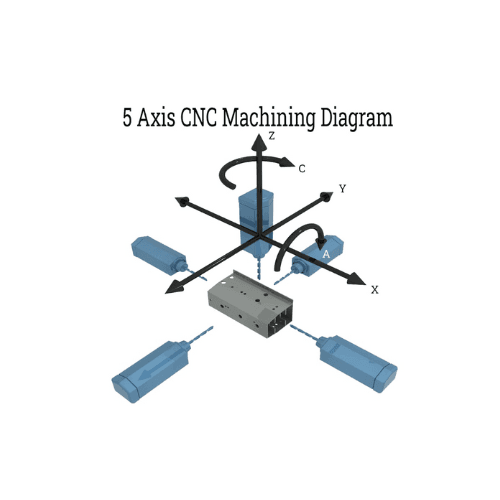
5-axis CNC machines are the most advanced, offering the highest level of precision and versatility. In addition to the X, Y, Z, and A axes, 5-axis machines add a fifth axis of rotation, often referred to as the B-axis.
- B-Axis: Rotation around the Y-axis.
Some key advantages of 5-axis machining include:
- Ability to machine complex, multi-sided parts in a single setup
- Improved surface finish and tighter tolerances
- Reduced setup time and increased efficiency
- Ability to machine undercuts and hard-to-reach areas
Applications:
5-axis machining is essential for creating complex, intricate parts that require machining on multiple sides with very tight tolerances. Industries such as aerospace, automotive, and medical device manufacturing heavily rely on 5-axis machining to produce parts with complex geometries.
Choosing the Right CNC Machining for Your Needs
When deciding between 3-axis, 4-axis, and 5-axis CNC machining, it’s essential to consider the complexity of the parts you need to produce, the precision required, and your production volume.
- 3-Axis: Best for simple parts and high-volume production.
- 4-Axis: Ideal for more complex parts that require machining on multiple sides with higher precision.
- 5-Axis: Necessary for the most intricate parts with complex geometries and tight tolerances.
Conclusion
In conclusion, understanding the differences between 3-Axis vs 4-Axis vs 5-Axis Milling is crucial for optimizing your manufacturing operations. While 3-axis machining is a cost-effective option for simple parts, 4-axis and 5-axis machining offer increasing levels of complexity, precision, and efficiency for more advanced manufacturing needs. The choice between these options will depend on the specific requirements of your parts and your overall manufacturing goals.
If you have any questions or need assistance in selecting the right CNC machining services for your business, feel free to reach out to our team at Witcool Machinery. We specialize in providing custom CNC solutions tailored to meet the unique demands of various industries. Visit our website at www.witcoolmachining.com to learn more.
FAQ
Q: What are the key differences between 3-axis, 4-axis, and 5-axis CNC machining?
A: The key differences lie in the number of axes along which the cutting tool can move. A 3-axis machine moves the tool along three axes (X, Y, Z), while a 4-axis machine adds a rotational axis (A-axis) to allow for machining on multiple sides without manual repositioning. A 5-axis machine adds a fifth axis (B-axis) for even greater flexibility, allowing complex geometries and intricate parts to be machined in a single setup.
Q: Which type of CNC machine should I choose for my project?
A: The choice depends on the complexity and precision required for your parts. A 3-axis machine is suitable for simple, flat parts, while a 4-axis machine is better for parts with features on multiple sides. If your project involves highly complex geometries or requires machining on multiple surfaces with tight tolerances, a 5-axis machine is the best option.
Q: How does 5-axis CNC machining improve manufacturing efficiency?
A: 5-axis CNC machining improves efficiency by allowing complex parts to be machined in a single setup, reducing the need for multiple setups and repositioning. This not only saves time but also enhances the precision and quality of the final product, as the part remains fixed in place during machining.
Q: What industries benefit most from 5-axis CNC machining?
A: Industries that require highly complex, precise parts benefit the most from 5-axis CNC machining. These include aerospace, automotive, medical device manufacturing, and complex mold-making industries, where intricate geometries and tight tolerances are essential.
Q: Is 4-axis CNC machining a good compromise between cost and capability?
A: Yes, 4-axis CNC machining offers a good balance between cost and capability. It allows for more complex parts to be machined compared to 3-axis machines while being less expensive than 5-axis machines. It’s ideal for projects that require machining on multiple sides but don’t need the full complexity of 5-axis machining.
Q: Can 3-axis CNC machines handle any complex parts?
A: While 3-axis CNC machines are primarily suited for simpler parts, they can still handle some level of complexity through multiple setups or by using specialized fixtures. However, for parts with intricate geometries or requiring machining on multiple faces, 4-axis or 5-axis machines are more efficient and precise.